Lynx 2000-2500 CNC Orbital Grinder
CNC Orbital Grinder
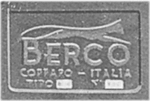
Lynx
crank and cam grinders line provides a completely new, simple and
flexible solution for grinding crankshafts and camshafts with a
single machine. Grinding main journals, crank pins or thrust faces
is achieved simply without an eccentric chuck. Both concave and
convex cam contours are obtained in a single clamping, without the
use of cam masters simply by using the Lynx software that controls
path machining of the contours.
L'evoluzione della specie
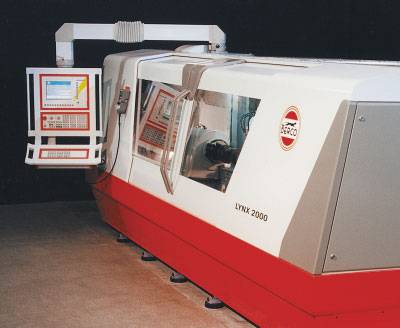
Lynx crank and cam grinders line provides a completely new,
simple and flexible solution for grinding
crankshafts and
camshafts
with a single machine. Grinding main journals, crank pins or thrust
faces is achieved simply without an eccentric chuck. Both concave
and convex cam contours are obtained in a single clamping, without
the use of cam masters simply by using the Lynx software that
controls path machining of the contours.
- A single machine for
crankshafts and
camshaft grinding.
- The most flexible solution for regrinding and for series
production.
- State-of-the-art technology.
- Friendly man-machine interface and very simple machine
operation.
- Effectiveness and cost saving.
Thanks
to the CNC and to specific software, crank pins and cam contours
(both negative and positive ones) are achieved by means of tabular
interpolation in the wheel head feed axis in consideration of the
angular position and the elevation value of the workpiece. This
technical solution enables the operator to achieve virtually any
contour, compatible with the grinding wheel shape and machine
geometry, by simple input of specific parametric data.
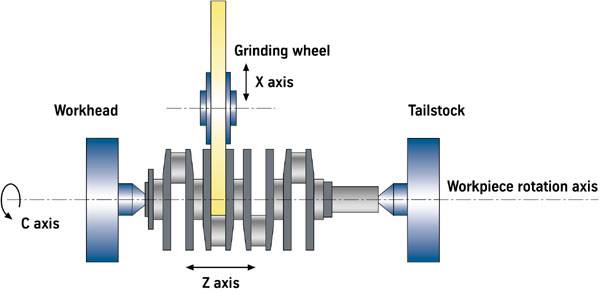
- A single machine for both
camshaft and
crankshaft grinding.
- Grinding crank pins, main bearings, thrust faces and
flywheel flanges in one clamping of the shaft rotating on its
centers.
- No need for any eccentric chuck thanks to the reciprocating
movement of the wheelhead.
- CNC path controlled machining enables contour grinding of
convex and concave cam contours in a single clamping and without
the need of cam masters.
Adding value to your
products
- Greater dimensional accuracy - roundness, straightness and
angularity - for crankpins, main journals and thrust flanges.
- Superior cam countouring precision.
- Excellent surface finish quality.
- High repeatibility.
- Tighter production tolerances.
The most flexible
solution for regrinding and for series production
- Single clamping grinding for both
camshaft and
crankshafts.
- Simple and easy-to-use man-machine interface with parametric
description of grinding cycles.
- Extremely easy control and operation of the machine, no need
for programming experts.
- Several grinding programs both in manual and automatic.
- Grinding wheel can be dressed into any shape.
- Easy changeover.
- Quick automatic set up.
- Easy integration with any external loading system and other
external measurement devices.
A wide choice of versions to satisfy all your
grinding needs
- Standard version with directdrive work-head, rotating
tailstock and manual clamping of the shaft.
- Production version with direct drive work-head, rotating
tailstock and automatic clamping for production of small-medium
size crankshaft and camshaft.
- Production version with
direct
drive work-head, motorized tailstock and automatic clamping by
means of retracting jaws for prodution of
medium-large size crankshaft.
- fixed tailstok and second "retractable"wheelhead for concave
cams grinding.
Effectiveness and Cost Saving
- Lower capital costs (one machine for both
crankshaft and
camshaft).
- Considerably reduced production times (single clamping).
- High cutting capacity.
- High productivity.
- Saving of production space.
- Minimized grinding tools costs.
- Low investment: minimum cost equipment suitable to your
grinding volume.
State-of-The-Art Technology
Machine Base
Lynx crank and cam grinders line has been developed using
sophisticated 3D modeling programs and
FEM analysis in order
to optimize the rigidity of the cast iron base and better dampen
vibrations.
- Unique one piece of cast Iron base.
- Optimized design for best damping characteristic.
- Very high strength and rigidity.
- A system for thermoregulation of the base ensures maximum
dimensional stability.
Wheelhead
- Lynx crank and cam grinders line features a motorized
spindle with an integral direct drive. Direct drive guarantees a
compact construction and improved dynamic rigidity.
- Fully automatic balancing system and vibration detector for
best cutting condition of the grinding wheel, higher accuracy
and quick changeover.
- Linear motor technology with direct drive of the X axis
(reciprocating movement of the wheelhead) resulting in improved
accuracy and higher rigidity of the hydrostatic drive train (no
transmission errors and wear effects).
- Full digital drive technology and a high resolution glass
scale guarantee excellent synchronization characteristics, fast
and accurate positioning, and high dynamics for rapid wheelhead
and table movement.
- Liquid cooled drives for best heat dissipation and zero
contamination.
- Rolling guides for high rigidity even in the most severe
applications.
- Linear encoder at the X axis resulting in min command
increment of 0.1µ.
Grinding wheels
Based on type of grinding Linx 2000can be fitted with:
- Conventional grinding wheels peripheral speed up to 35m/s,
ideal for the production of small batches.
- Sintered ceramic grinding wheels-speed up to 63m/s offering
higher resistance to wear and providing high removal capacity
suitable for large size batches.
- highly productive CBN (cubic Boron Nitride) grinding
wheels-speed up to 120m/s-for maximum machining capacity ,
tighter tolerances and particularly suitable for series
production.
Workhead
- Chatter free grinding produces a perfect surface quality. We
have designed a
motorized
spindle to achieve this with a direct drive to the
C-axis.
- Direct drive of the workpiece spindle guarantees a compact
construction, improved accuracy, reliability and higher rigidity
of the drive train (no transmission errors and wear effects).
- Full digital drive technology and a high resolution rotary
encoder guarantee excellent synchronization characteristics and
high dynamics.
- Liquid cooled drive for best heat dissipation and zero
contamination.
- Rolling guides for high rigidity even in the most severe
applications.
- Encoder at the C axis resulting in min command increment of
0,0001 deg.
- Spindles with manuals clamping, automatic clamping and
automatic
clamping by means of retractable jaws in order to
satisfy any possible grinding need.
Tailstock
- Optimized dimensions and solidly bolted on the table for
maximum rigidity.
- Slide mounted tailstock with 50mm stroke is able to
accommodate complete workpiece families without the need to
re-set.
- It features a hydraulic quill retraction by foot pedal for
easy workpiece clamping.
- Rotating
tailstock with rolling bearing, motorized tailstock and
fixed
tailstock for concave cams grinding are available.
Work-table
- Linear motor technology with direct drive of the Z axis
resulting in high dynamics, improved accuracy, higher
reliability and rigidity of the drive train (no transmission
errors and wear effects).
- Full digital drive technology and a high resolution linear
encoder guarantees excellent synchronization characteristics,
fast and accurate positioning, and high dynamics.
- Min command increment of 0.1µ.
- Linear rolling guides ensure higt rigidity even in the most
severe applications and prevent the "backlash" phenomenon
typical of hydrostatic systems.
Optional Equipment
- Wide range of
"follow down"
hydraulic steady rests to accomodate shaft diameters
from 20 to 125 mm.
- Marposs
measuring
device for "in-process" control of main bearings, crank
pin diameters.
- A second
Retractable wheelhead for grinding concave cams. It
features direct drive motor which enables installation of
grinding wheels with a diameters from 38 to 100 mm.
- A cartesian
manipulator (gantry) enables automatic workpiece loading
and unloading.
- A cooling and cooling-lubrication device.
CNC
- Simple program input via keyboard, tape or disk.
- Background editing and programming for increased
productivity.
- Gauging of main and crank pins diameter and thrust faces,
enable crankshaft measuring and generation of the grinding
cycle.
- Contour gauging enables cam profile mapping and grinding
profile generation without the need of the cam master.
- Cam profile and the valve opening curve can also be
varied/corrected via CNC built in functions.
Operating Controls
- The intuitive, ergonomic and logical arrangement of the
operating control
ensures most convenient operation.
- The
portable PCU-terminal enables machine operation in safe
conditions while closely checking on the grinding operation.
Safety Features
Safe operation is ensured by
- Touch
detector for continuous monitoring of the contact
between grinding wheel and workpiece, grinding wheel and
dressing device results in minimal non-cutting times. The device
works also as Integrated collision detection system.
- The wheel spindle drive motor control incorporates a load
meter so that if the pre-set limits are passed, an overcurrent
condition will initiate an emergency stop.
- Two front sliding doors for full enclosure of the working
area during machine grinding operation.
- During loading/unloading of the workpiece (front doors are
open), two fences/panels automatically separate the working area
from the wheelhead (that slides all the way back along the X
axis) and the operator is fully protected even with the grinding
wheel rotating.
- Lynx2000 has been built according with the CE norms and EMC
directives regulating manufacture of machine tools.
- All safety features have been arranged in such a way as not
to hinder the ergonomy of the machine and the production of the
operator.
Grinding
Simple and easy-to-use
man-machine interface with
parametric description of
grinding cycles.
Extremely easy control and operation of the machine, no need for
programming experts.
Comfortable operation by means of Lynx software programs and
operator support by easy to use menu technique.
Control and simulation of the generated grinding cycle in real time.
- Manual & automatic.
- Cylindrical grinding (oscillation of the table on the Z
axis).
- Plunge cut and multi-plunge cut grinding.
-
Orbital grinding of crankshafts (reciprocating of the
wheelhead on the X axis following the workpiece rotation on the
C axis).
- Cam contour grinding.
-
Concave Cam grinding, with
2nd grinding
wheel.
- CAMVIEW is a specific
program that enables the operator to view the difference between
the theoretical and actual contour of the cam. With this utility
it is possible to modify the deviation between the two curves by
also calculating and viewing the effect it will have on the
valve opening law.
Wheel Dressing Programs
Wheel dressing device via CNC to obtain almost
any grinding wheel
profile. The radius can be dressed both on left and on right
wheel sides, for straight or angular infeed. The file with the
dressing program to shape the wheel can also be imported via
external interface.
Graphical generation and simulation of the grinding wheel profiling
operation is standard.
Available functions:
- Dressing compensation.
- Compensation of the grinding wheel diameter.
Dressing Options
The operator has various possibilities to select the time for
dressing:
- After the programmed switchover points.
- After a programmed number either of machined parts or of
grinding operations.
Dressing Device
- Three dressing devices (for front, right and left side)
installed on the tailstock.
-
Rotating diamond wheel (available upon request).
We Care
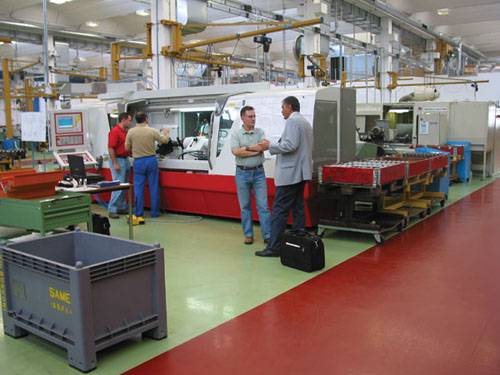
Service
After your decision for investment, Berco will always be standing by
with their quick and competent After Sales Service. Expert
technicians will be able to solve your problems while an efficient
logistic organization will be able to quickly deliver spare parts
wherever you need them.
Maintenance
- Accurate and precise manuals.
- Easy access to complete interior.
- Easy to service.
- Operator friendly for flexible grinding.
- Modular structure.
- Improved maintainability.
Leadership in environmental development
Not only do we care about our customers, supplying quality machines
manufactured since '91 under
ISO9001
certified process, but we also care about the environment. Since Jan
2000, Berco is
ISO14001 certified and has adopted Environmental Procedures
throughout the entire manufacturing process. We have an
Environmental Strategy and we continuously check on the progress
made toward the set objective.
orkpiece
|
Lynx 2000 |
Lynx 2500 |
Lynx 2500 HD |
Max grinding diameter in
orbital grinding = Dp+S (#) |
mm 220 |
mm 300 |
mm 400 |
Max grinding diameter in
cylindrical grinding |
mm 300 |
mm 300 |
mm 400 |
Max. swing over table |
mm 300 |
mm 300 |
mm 400 |
Steady rest min./max. diameter (*) |
mm 20/125 |
mm 20/125 |
mm 20/125 |
Max. workpiece weight
between centers |
kg 135 |
kg 200 |
kg 400 |
Centers height |
mm 270 |
mm 270 |
mm 310 |
Max. distance between centers |
mm 1700 |
mm 2500 |
mm 2500 |
Max. grinding length
(tailstock with rolling bearings*) |
mm 1500 (1300*) |
mm 2500 |
mm 2500 |
Self-centering chucks diameter |
mm 180/210/260 |
mm 180/210/260 |
mm 180/210/260 |
Slide mounted tailstock stroke |
mm 50 |
mm 50 |
mm 50 |
Automatic Balancing Device |
Programmable |
Programmable |
Programmable |
(#) Dp = crank pin diameter;
S = pin stroke
(*) Option |
Grinding Wheel
|
Lynx 2000 |
Lynx 2500 |
Lynx 2500 HD |
Max. Diameter |
mm 660 |
mm 660 |
mm 850 |
Min./Max. Width |
mm 20/80 |
mm 20/80 |
mm 20/80 |
Max. Surface Speed |
m/sec 35/63/120 |
m/sec 35/63/120 |
m/sec 35/63/120 |
Wheelhead (X axis)
|
Lynx 2000 |
Lynx 2500 |
Lynx 2500 HD |
Drive and guideway |
Linear Motion System |
Linear Motion System |
Linear Motion System |
Stroke |
mm 490 |
mm 490 |
mm 490 |
Positioning system |
Optical |
Optical |
Optical |
Min. input increment |
mm 0.0001 |
mm 0.0001 |
mm 0.0001 |
Workhead (C axis)
|
Lynx 2000 |
Lynx 2500 |
Lynx 2500 HD |
Workpiece speed rotation
range |
rpm 1-1000 |
rpm 1-1000 |
rpm 1-1000 |
Workpiece speed rotation
range for contour grinding |
rpm 1-400 |
rpm 1-400 |
rpm 1-400 |
Torque at spindle |
Nm 250 |
Nm 250 |
Nm 250 |
Positioning system |
Encoder |
Encoder |
Encoder |
Min. input increment |
deg. 0.0001 |
deg. 0.0001 |
deg. 0.0001 |
Table (Z axis)
|
Lynx 2000 |
Lynx 2500 |
Lynx 2500 HD |
Drive and guideway |
Linear Motion System |
Linear Motion System |
Linear Motion System |
Positioning system |
Optical |
Optical |
Optical |
Min. input increment |
mm 0.0001 |
mm 0.0001 |
mm 0.0001 |
Drive motors
|
Lynx 2000 |
Lynx 2500 |
Lynx 2500 HD |
Grinding wheel spindle
(built in direct drive) |
kW 25 |
kW 50 |
kW 50 |
Workpiece spindle
(built in direct drive) C axis |
kW 7 |
kW 7 |
kW 7 |
General Data
|
Lynx 2000 |
Lynx 2500 |
Lynx 2500 HD |
Width A |
mm 5500 |
mm 7680 |
mm 7680 |
Depth B |
mm 2600 |
mm 2600 |
mm 2600 |
Height C |
mm 2000 |
mm 2100 |
mm 2100 |
Weight |
kg 11000 |
kg 15000 |
kg 15000 |
Are you trying to inquire about a part
or check availability of a product or a solution service?
Please either call / WhatsApp (60) 19 333 9484 at or email us at
wso@assurich.com.my
or submit an enquiry form
online. |
|