WS7

Working Diameters
With Standard Equipment
IN-LINE BORING
Starting from ø 400 mm to over ø 1200 mm
OVERLAY WELDING
Internal– from ø 350 mm to over ø 1200 mm
External- from ø 100 mm to over ø 1200 mm
Accessory kits
KIT 2000 from ø 120 mm to ø 1200 mm
For facing bosses, creating circlip grooves, external machines.
Upon request, we can supply:
• Special kits for working on diameters inferior to 400 mm
• Personalized kits for specific machining or applications.
Photo Gallery
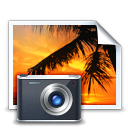
WS7
Video gallery application
•
Facing head WS7
•
Welding WS7
•
Set-Up: In line borning
• Set-Up: Overlay welding
• Set-Up: Centering
Machine Size
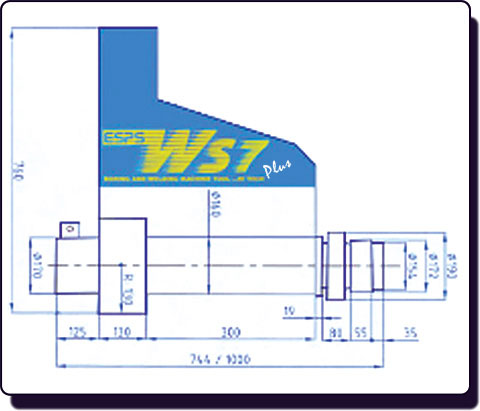
Technical
Characteristics |
The machine is equipped with an
electronic control panel with diagnostic display. |
TOOL HOLDER SHAFT DIAMETER |
mm
|
100 ( 3,94
in ) |
TOOL HOLDER SHAFT LENGTH |
mm |
3000 mm
single shaft (potentially connectable) |
BORING DIAMETER |
mm
|
400 - 1200
( 15,75 in - 47,24 in ) |
WELDING DIAMETER |
mm
|
350 - 1200
( 13,78 in – 47,24 in ) |
WELDING TECHNOLOGY |
|
SPIRAL
(CONTINUOUS WITH VARIABLE STEP) |
LONGITUDINAL STROKE |
|
UNLIMITED
WITH STEP OF 260 mm (10,24 in) |
ROTATION MOTOR |
|
C/C (CE
COMPLIANT) |
FEED MOTOR |
|
C/C (CE
COMPLIANT) |
FEED SYSTEM |
|
ELECTRIC-MECHANICAL |
OUTPUT TORQUE AT THE BAR |
|
4200 Nm (41
rpm) |
MAX
ROTATION SPEED |
rpm
|
41
|
FEED RATE |
mm
/ rpm |
0 - 0,4 ( 0 -
0,02 in / rev ) |
MAX
FEED SPEED(w/rapid button) |
mm
/ min |
53
|
REMOVAL MATERIAL |
cm3
/ min |
172
|
DRIVE UNIT WEIGHT |
Kg
|
105
|
Standard Equipment |
N°1 DRIVE
UNIT |
N° 1 CONTROL PANEL |
N° 1 CABLE
FOR CONTROL PANEL |
N° 1 CONTROL PANEL HOLDER |
N° 1 TOOL
HOLDER SHAFT ø 100 mm Lgth. 3000mm |
N° 4 BEARING CARRIERS,
|
N° 34
BRACKETS FOR ADJUSTING DIAMETERS (N° 12 X mm 200, N° 12 X mm
300, N° 10 X mm 700 double special brackets) |
N° 2 STAR SHAPED BRACKETS ø
700 mm |
N° 20 WASHERS
FOR STAR SHAPED BRACKETS FIXING |
N° 10 STUD FOR BRACKET |
N° 10 STUD
SPACERS |
N° 10 STUD NUTS |
N° 20 WASHERS
18 |
COMPLETE BOLTING |
N° 1
CENTERING KIT (2 EXT.RINGS – 2 INT.RINGS - 6 BOSSES Lgth.
100 mm) |
N° 18 THREADED BARS FOR
CENTERING KIT (6 – M30x200 mm; 6 – M30x400 mm; 6 – M30x600
mm) |
N° 10 CARBIDE
INSERTS |
N° 1 TOOL HOLDER S10Cx30 mm
(COMPLETE WITH WRENCH AND TORX SCREW) |
N° 1 TOOL
HOLDER S10Cx50 mm (COMPLETE WITH WRENCH AND TORX SCREW) |
N° 1 TOOL HOLDER S12Cx80 mm
(COMPLETE WITH WRENCH AND TORX SCREW) |
N° 1 MAIN
DISK SHAPED TOOL HOLDER ø 340 MM COMPOSED OF 2 HALF DISKS |
N° 1 TOWER SHAPED TOOL
HOLDER EXTENSION 100 MM FOR MAIN TOOL HOLDER |
N° 1
SUPPLEMENT HEIGHT 50 MM FOR TOOL HOLDER EXTENSION |
N° 2 SUPPLEMENTS HEIGHT 100
MM FOR TOOL HOLDER EXTENSION |
N° 1 CHROMED
BAR ø 40 LGTH 50 MM FOR TOOL HOLDER EXTENSION |
N° 1 CHROMED BAR ø 40 LGTH
100 MM FOR TOOL HOLDER EXTENSION |
N° 1 CHROMED
BAR ø 40 LGTH 150 MM FOR TOOL HOLDER EXTENSION |
N° 24 THREADED BARS M14
(TENSION BAR) FOR TOOL HOLDER (4 X100mm + 4 x 150 mm + 4x
200mm + 4 x 250 mm + 4 x 300 mm + 4 x 350 mm) |
N° 2 TOOL
HOLDER KEYS 8X8X110 |
N° 1 MICROSPAND (MODULAR
DEVICE USED FOR INTERNAL MEASUREMENTS) |
n° 1
MICROSPAND EXTENSION 100 mm |
N°1 COMPARATOR 1/100
|
N°2
COMPARATOR HOLDER 8/8 – 10/8 |
N°1 COMPARATOR EXTENSION |
N° 1 WELDING
TORCH CABLE WITH EUR-FITTING |
N° 1 TORCH SHAFT ø 40 mm
Lgth. Tot. 2000 mm |
N° 2 ADAPTING
BUSHINGS FOR TORCH SHAFT lgth. 240 – lgth. 130 |
N° 3 TORCH-HEADS FOR
INTERNAL OVERLAY WELDING C/W WELDING WIRE NOZZLES AND GAS
DIFFUSER (B 125 mm + G 180 mm + I 250 mm) |
N° 4 TORCH
HEAD EXTENSIONS (D 55 mm + E 45 mm + H 135 mm + L 160 mm) |
N° 2 SHORT WELDING WIRE
NOZZLES ø 1 mm |
N° 6 LONG
WELDING WIRE NOZZLES N° 2 – ø 0,8 mm; N° 2 – ø 1 mm; N°2 – ø
1,2 mm |
WRENCHES |
OPERATION
MANUAL |
N° 1 TROLLEY (for
containing all the standard kit) |
Equipment upon Request
KIT |
|
KIT 2000/ ø
100
from ø 120 to ø 1200 mm |
For
facing bosses, creating circlip grooves, external machining
Composed of:
· N° 1 gear box
· N° 5 spacers |
CERTIFIED TEST – STEEL C45
DIAMETER |
mm |
Ø 600 |
Ø 1200 |
CUTTING DEPTH |
mm |
5 in
the radius
10 in the diameter |
2 in
the radius
4 in the diameter |
FEED SPEED |
mm/min. |
5 |
3 |
Control Panel An electronic circuit has been inserted
to guarantee a major safety in operation and to safeguard the rotation motor
from excessive strain in case of an incorrect setup of the parameters, as well
as to compensate possible critical points in machining. It automatically and
proportionally reduces the feeding speed to reach the maximum strain point of
the rotation motor, in order to dynamically reduce the load of the work, without
passing the stop point for protection.
Thanks to the led bar called STP, it is possible to constantly monitor the
motor’s work load, so to be able to optimize the choice of the parameters
(rotation speed and feed speed), based on the hardness of the material, the
type of tool being used, to the machining diameter and to routing diameter of
the tool. Furthermore, the bar signals in advance the alarm condition and the
subsequent shut down of the control panel, flashing until the working conditions
are restored.

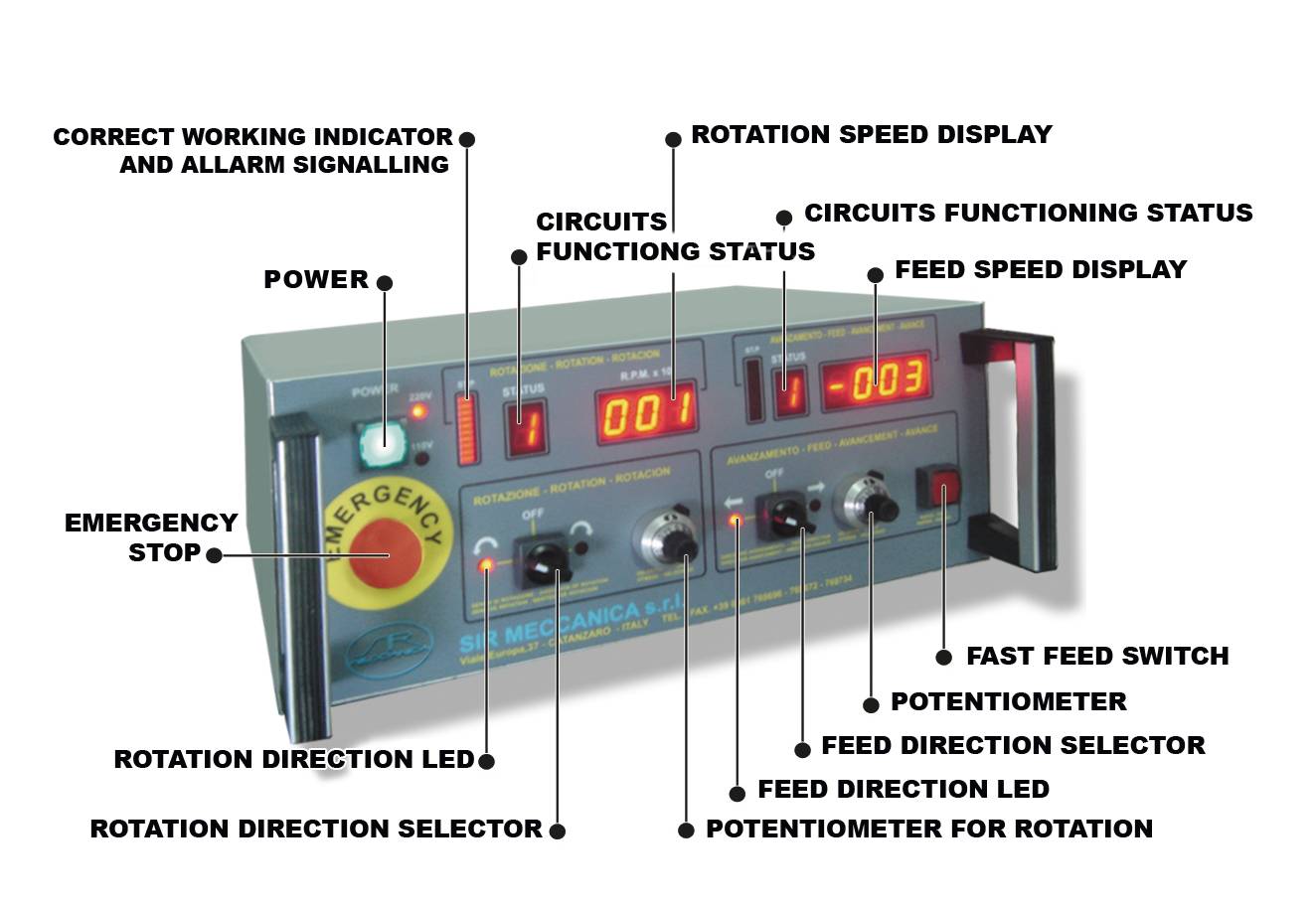
The technical characteristics include:
AC 110 ~ 220 50 / 60 HZ WITH AUTOSELECTION OF MAINS VOLTAGE,
WITHOUT THE USE OF TRANSFORMERS OR INVERTERS; ELIMINATING
ELECTROMAGNETIC INTERFERENCES
ESPS ® TORQUE ELECTRONIC RUNNING OF THE TWO MOTORS WITH
ELECTROMECHANIC SYNCHRONIZATION
DISPLAY FOR SPEED OF ROTATION REVOLUTIONS
ACOUSTIC WARNING WITH DISPLAY WITH FIGURED SIGNALS OF POSSIBLE
FAULTS DURING THE RUNNING OF THE ROTATION MOTOR
DISPLAY FOR SPEED OF FEEDING REVOLUTIONS
ACOUSTIC WARNING WITH DISPLAY WITH FIGURED SIGNALS OF POSSIBLE
FAULTS DURING THE RUNNING OF THE FEEDING MOTOR
MAIN SWITCH
EMERGENCY SWITCH
INVERTER DX/SX FOR FEEDING
INVERTER DX/SX FOR ROTATION
POTENTIOMETER FOR ROTATION REGULATION
POTENTIOMETER FOR FEEDING REGULATION
SWITCH FOR RAPID TRANSLATION OF THE SHAFT
Are you trying to inquire about a part
or check availability of a product or a solution service?
Please either call / WhatsApp (60) 19 333 9484 at or email us at
wso@assurich.com.my
or submit an enquiry form
online. |
|